3d-Druck Technologien

SLS Selektives-Lasersintern
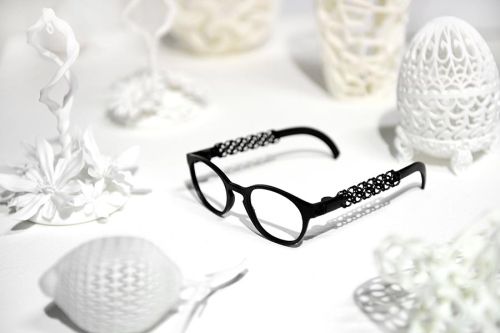
Das Verfahren
Beim Sinter- und Schmelzverfahren handelt es sich um ein Verfahren lokalen Aufschmelzens von pulverförmigem Ausgangsmaterial durch eine Energiequelle (z.B. Laser). Der Werkstoff wird schichtweise auf eine Teileplattform aufgebaut (Pulverbett) und erstarrt nach der Abkühlung zu einem festen Körper. Das Besondere dabei ist, dass im Gegensatz zu den konventionellen Fertigungsmethoden sehr komplexe und stabile dreidimensionale Geometrien – auch mit Hinterschneidungen – in relativ kurzer Zeit erzeugt werden können. SLS ist eines der produktivsten 3D-Druckverfahren und wird genutzt, um Funktions-Prototypen oder Kleinserien zu fertigen. Druckteile mit hoher Flexibilität bei dünnen Wanddicken und großer Festigkeit bei zunehmender Wanddicke mit unterschiedlichen hochwertigen Thermoplasten.
Materialien
PA6 | PA11 | PA2200 | PA2210 FR (Flammhemmend) | PA2241 FR | PP | PS Primecast® 101 | TPU | HT-23 (Polyetherketonketon) | Alumide® (PA12 mit Aluminiumpulver gefüllt)
Anwendungsbereiche I
Prototypen
Lasersintern bietet sich hervorragend im Bereich Rapid Prototyping an. Sehr oft wird da Verfahren dazu verwendet, spätere Spritzgussbauteile vor der Werkzeugherstellung auf die Passform hin zu überprüfen.
• Einbaumuster
• Funktionsprototypen
• Anschauungsmodelle
Funktionsteile
Die ausgewogene mechanischen Eigenschaften unserer Materialen erlauben es, langlebige und robuste Bauteile für viele Einsatzbereiche herzustellen. Die neutral weiße Basis eines SLS Bauteils eignet sich hervorragend für die Veredelung im Falle von Sichtbauteilen.
• Fertigungshilfen, Lehren usw.
• Technische Sonderbauteile
• Orthesen und Prothesen
Anwendungsbereiche II
Kleinserien
Für kleine Bauteile, die in niedrigen bis mittleren Stückzahlen (1 – 10.000 Stk.) benötigt werden ist SLS perfekt geeignet. Durch den Einsatz industrieller 3D-Drucker ist ein hoher Durchsatz mit kurzen Lieferzeiten garantiert.
• Anbauteile im Maschinenbau
• Abdeckungen und Gehäuse
• Konsumgüter
Vorteile
• Es sind keine Stützstrukturen notwendig
• Sehr breites Anwendungsfeld
• Maßhaltige Bauteile
• Hohe Temperaturbeständigkeit
• Dicke Wandstärken möglich
• Materialien für Brandschutzausrüstung oder für Luftfahrtanwendungen
• Bauteile können in jede Farbe eingefärbt werden
• Zahlreiche Veredlungsmöglichkeiten
Nachteile
• Unbehandelte Oberfläche leicht rau
• Bauteile können nicht durchgefärbt werden
• Dünne Wandstärken sind nicht dicht, können aber nachträglich mit Dichtol druckdicht gemacht werden.
• Nicht vollständig isotrope Eigenschaften (x-y stärker als z)
• Verzugsanfällig
OPTION
Oberflächenbehandlung

SLA Stereolithografie
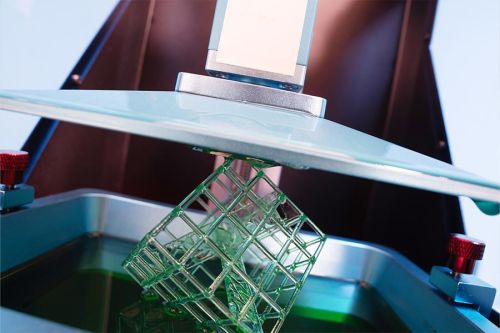
Das Verfahren
Das Licht kann entweder von oben auf die Flüssigkeitsoberfläche oder von unten durch den Boden des transparenten Bassins gestrahlt werden. Sobald eine Schicht des Kunstharzes durch das UV-Licht ausgehärtet ist, wird das Modell entweder nach unten in das Bassin (falls das Licht von oben kommt) oder nach oben aus der Flüssigkeit (bei Lichteinfall von unten) gezogen. Dieser Prozess wird solange wiederholt bis das Modell fertig ist.
Typischerweise müssen bei dieser Methode zusätzliche Stützstrukturen in Form von dünnen Stäbchen eingebaut werden, die überhängenden Teilen Halt verleihen. Diese können später durch Herausbrechen oder –Schneiden entfernt werden.
Materialien
Kunstharz | Wir bieten auch transparentes Kunstharz an.Anwendungsbereiche
- Hochauflösende Bauteile
- Bauteile mit feinen Details
- Große Bauteile
- Designmodelle
Vorteile
- Große Modelle und Modelle mit Hohlräumen möglich
- Gut zur individuellen Oberflächengestaltung geeignet – siehe Veredelung
- Glatte Oberflächen auch ohne Nachbearbeitung
- Schnelle Umsetzung von Prototypen bereits in frühen Phasen der Produktentwicklung
- Herstellung sowohl von flexiblen, als auch starren 3D-Objekten
- Kostengünstige Produktion
- Gut zum Finischen und Lackieren geeignet
- Mehrteilige Baugruppen möglich
Nachteile
- Je nach Material können Bauteile spröde sein
- Stützstrukturen können die Konstruktionsfreiheit einschränken
- Bauteile sind nur eingeschränkt UV-beständig
- Teilweise geringere Temperaturbeständigkeit als andere Verfahren (Sondertypen mit höherer Temperaturbeständigkeit auf Anfrage verfügbar)
OPTION
Oberflächenbehandlung
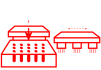
MJF Multijet Fusion
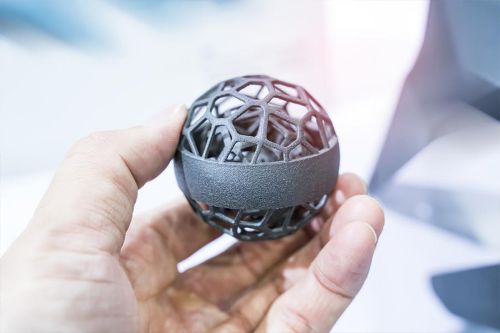
Das Verfahren
Multi Jet Fusion (MJF) ist ein pulverbasiertes 3D-Druck-Verfahren, mit dem hochauflösende und präzise 3D-Objekte mit geringer Porosität und hoher Oberflächengüte produziert werden. Im Gegensatz zum selektiven Lasersintern (SLS) wird beim MJF vollständig auf den Einsatz von Laserstrahlung verzichtet und als Energiequelle Infrarotlicht eingesetzt. Dank schnellerer Druckvorgänge und den daraus resultierenden kürzeren Maschinenzeiten können beim Multi Jet Fusion Verfahren auch sehr feine Schichtstärken wirtschaftlich produziert werden.
Neben der deutlichen Zeitersparnis punktet das Multi Jet Fusion-Verfahren durch hervorragende Bauteilqualität: Mit 1.200 dpi erreichen die Anlagen auf der X-Y-Achse eine Auflösung, mit der Objekte auf Spritzguss-Niveau gefertigt werden können.
Materialien
HP-PA12 | HP-PA 11 | TPU 90A
Anwendungsbereiche
- Funktionelle Prototypen
- Kleinserien
- Belastbare, serientaugliche Einzelstücke
Vorteile
- Hohe Baugeschwindigkeit
- Hohe Verschleißfestigkeit
- Bauteile erreichen eine hohe Dichte und geringe Porosität
- Ideal für die Herstellung von Prototypen mit funktionalen und mechanischen Eigenschaften
- Preiswerte Alternative für Kleinserienfertigung
- Ermöglicht eine Schichtdichte von 80 Mikrometern (gute Detailtreue)
- Extrem dünnen Schichten ermöglichen eine exzellente Oberflächenqualität
Nachteile
- Leicht raue Oberfläche (bedingt durch Pulverkorngröße)
- Mittlere Detailabbildung
- Leicht fleckige Bauteile
- Neigt zu Einfallstellen bei dicken Wandstärken
OPTION
Oberflächenbehandlung

FDM Extrusionsverfahren
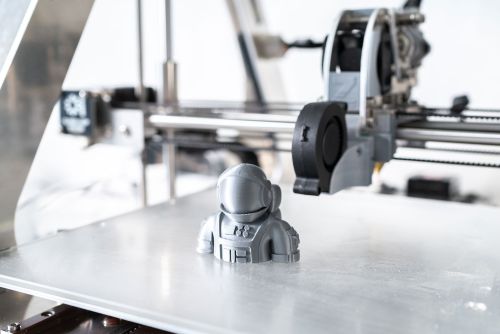
Das Verfahren
Fused Deposition Modelling (FDM) oder Fused Filament Fabrication (FFF) bietet die größte Materialvielfalt im 3D-Druck. Das Druckteil wird Schicht für Schicht aus geschmolzenem Kunststoff oder aus in Kunststoff eingebettetem Metallpulver aufgebaut. Bei diesem Verfahren sind auch die größten Bauteile möglich. Voluminöse Bauteile und Prototypen sowie Serienbauteile im nicht-sichtbaren Bereich könne so kostengünstig verwirklicht werden. Das Verfahren ist die am weitesten verbreitete 3D-Druck Technologie.
Materialien
ABS | ABS/PC | ASA | PC | PET-G | PLA | Nylon | Nylon-CF | Ultem 1010 | Ultem 9085 | TPU
Anwendungsbereiche I
- Präzise Bauteile für anspruchsvolle Tests und raue Umgebungen
- Befestigungsteile, -Werkzeuge und -Prototypen
- Luft- & Raumfahrt
- Automobilbranche
- Große Bauteile
Vorteile
- Kostengünstigstes 3D Druck-Verfahren auf zwei Ebenen
- Schnelles additives Verfahren geeignet für Rapid Prototyping und für Kleinserienfertigung
- Konstante Weiterentwicklung wegen hoher Verbreitung der Technologie
- Serienähnliche Materialen (weitgehend chemisch ident)
Nachteile
- für eine hohe Oberflächengüte ist eine Nachbearbeitung notwendig
- Gefahr von unzureichender Schichthaftung
- Strukturen/Schichten die feiner als die Extrusionsbreite sind, können nicht dargestellt werden.
- Anisotrope Materialeigenschaften
OPTION
Oberflächenbehandlung
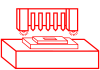
PolyJet Verfahren
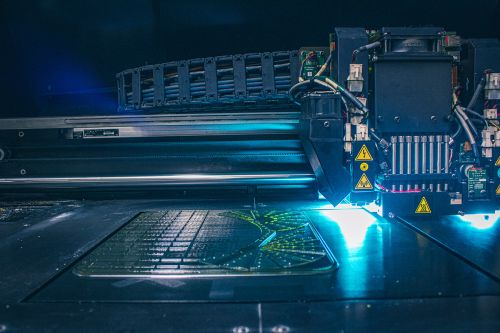
Das Verfahren
Beim Polyjet Druckkopf-Lampenverfahren wird das Photopolymer über mehrere Druckköpfe schichtweise auf die Bauplattform aufgetragen und mit Hochenergielampen verfestigt. Die minimale Schichtdicke liegt bei ca 0,012 mm!
Der 3D-Druck nach dem PolyJet- oder MultiJet-Verfahren gilt aufgrund der hohen Maßhaltigkeit und hybriden Materialmöglichkeiten der produzierten Bauteile als High-End-Lösung im Bereich der additiven Fertigungsverfahren. Die Methode sticht durch die große Vielfalt an Materialien hervor, die auf effiziente Weise in einem einzigen Objekt integriert werden können.
Materialien
Full Cure 720 | ABS-like | Tango (Rubber-like) | Vero-Clear (transparent) | MED610
Vorteile
- Sehr große Materialvielfalt (von fest bis gummielastisch)
- Transparente Bauteile
- Verbundmaterialien herstellbar
- Hohe Genauigkeit und Oberflächenqualität
- Schnelles Verfahren, da keine Aufheiz- und Abkühlzeiten benötigt werden
- Herstellung von 3D-gedruckten Spritzgießkavitäten aus Kunststoff
- Gute Nacharbeitsmöglichkeiten
Nachteile
- Geringere Temperaturbeständigkeit (Sondertypen mit höherer Temperaturbeständigkeit auf Anfrage verfügbar)
- Materialien leicht spröde
- Materialien nicht UV-beständig (Versprödung und Verfärbung möglich)
- Teilweise Einschränkungen in der geometrischen Freiheit speziell bei filigranen Bauteilen, da das Stützmaterial mit Wasserstrahl entfernbar sein muss (Zugänglichkeit, Beschädigungsgefahr)
OPTION
Oberflächenbehandlung

Pulver-Binder Verfahren | 3D Printing (3DP)
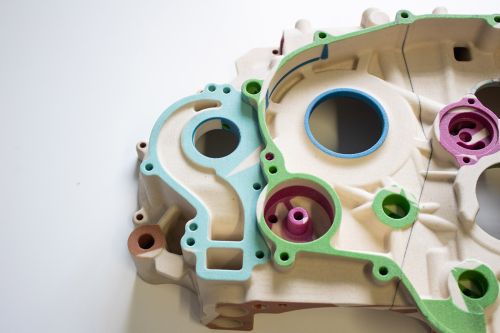
Das Verfahren
Mit dem Pulver-Bindeverfahren wird beim 3D-Printing (3DP), ähnlich wie beim Selektiven Lasersintern, das pulverförmige Ausgangsmaterial schichtweise aufgetragen.
Um das Pulver zu verfestigen und die einzelnen Schichten zu verbinden wird über einen Druckkopf ein flüssiger Binder auf den Schichtquerschnitt des Bauteils aufgedruckt. Die so verklebte Pulverschicht wächst Schicht für Schicht im Pulverbett heran und wird gleichzeitig durch das überschüssige Pulver gestützt. Somit sind keine zusätzlichen Stütz- und Supportstrukturen notwendig.
Materialien
Polymergips
Anwendungsbereiche
- Mehrfarbige Bauteile mit vollem CMYK-Spektrum
- Bauteile mit Farbverläufen
- Architekturmodelle
- Figurenmodelle
Vorteile
- Kompliziert Geometrien möglich
- Hohlräume möglich
- Vielfarbige Bauteile mit vollem CMYK-Spektrum in einem Bauvorgang
- Sehr hohe Baugeschwindigkeit, kurze Lieferzeiten
- Wandstärken und freitragende Elemente ab 2 – 4 mm, Details ab 1,0 mm.
- Umweltfreundlicher 3D Druck, durch Recycling des ungenutzten Gips-Materials und Verarbeitung bei niedrigen Temperaturen
Nachteile
- Für eine hohe Oberflächengüte ist eine Nachbearbeitung notwendig
- Durch die schichtweise Fertigung kann es zum Bruch der Modelle kommen
- Keine ausreichend mechanischen Festigkeiten. Es muss nachträglich infiltriert werden.
OPTION
Oberflächenbehandlung